PLASTIC PACKAGING FILM PRODUCTION PROCESS FOR DIFFERENT TYPES OF MATERIALS
Plastic bags, also known as plastic packaging in the manufacturing industry today, can be found easily anywhere in the world. With the great benefits and super cheap prices of the inventors that in recent decades, we can see that plastic packaging has become an essential product of modern life before the concerns about their impact on the environment is formed.
We use them to store everything in this world, from food, to packaging confectionery or even to storing industrial goods in large volumes,... So the process to produce a bag How does nylon work? It's really not too complicated, let's read together with Sunrise Colors to learn the elements that make up the PLASTIC PACKAGING FILM PRODUCTION PROCESS FOR DIFFERENT MATERIALS.
The 4-step process of producing plastic packaging
To ensure the criteria of product quality as well as safety for users, especially when used to store foods, plastic packaging companies have created a 4-step process of safe production. Safe and hygienic with quality inputs.
1. Mixing materials:
In this step, the technician will start to mix the plastic granules into a specialized hopper or mixing tank. These plastic granules can be 100% virgin plastic or mixed in proportion with recycled plastic depending on the purpose of production. Characterization additives are also added in this step.
2. Film forming, blowing film:
After mixing, the raw material mixture is scooped out to put into the extruder or can also use a straw directly. From here the mixture is melted and blown up into a bubble as the cylinder is pointed upwards. The shell of this bubble is a nylon membrane. In this step, the machine operator will align the thickness and width of the nylon film by specialized techniques.
3. Rolled into plastic rolls:
After the extrusion-blowing process, this layer of plastic bubbles is pulled up to cool, then run through a series of rollers to be pressed into a flat form. Finally they are rolled into a paper or plastic core. Up to now, we have a product that is a double film nylon roll. For single film, the roll forming process will have an additional stage of stripping this double film into 2 and wrapping 2 paper cores at the same time.
4. Cut into plastic bags:
This is the last step of the process. The nylon roll is put into the automatic cutting machine. The sensor eyes on the machine will accurately measure the length needed to split the nylon roll into equal segments. The bottom of the plastic bag is also heat-sealed by the heat press system integrated on the cutter.
The production process of each type of plastic is different
In general, plastic bags or any plastic products are made from plastic beads. In addition to classifying them according to primary and recycled plastic beads, there are many types of plastic beads, each of which has relatively different properties and characteristics. In the field of plastic packaging production, the most popular are still plastics such as LDPE, HDPE, PP, PE, OPP, ... So the production process for each type of plastic is also somewhat different.
Production process for LDPE
LDPE plastic beads are characterized by good flexibility and transparency. This type has high elasticity along with very good resistance to water, chemicals and solvents, especially safe for food. Some typical examples for LDPE plastic packaging such as plastic bags filled with broth, sugarcane juice, packaging of spices, sugar, salt, ... are sold in markets.
The production process of LDPE packaging is completely similar to the basic extrusion-blowing steps of the plastic bag production process. This material has a melting point of about 105-115°C.
LDPE plastic bags are easy to print but difficult to punch due to the flexible nature of this plastic. In addition, this material is also a good insulator, but it is prone to electricity, if used to store electronic components or in an explosive environment, it is necessary to treat the surface with anti-static.
Production process for HDPE
HDPE bags or industry insiders, or HD plastic for short, have moderate and medium clarity and surface gloss. This type of plastic material is hard, not flexible, LDPE plastic. The bags with handles that we often use to store products bought from markets or stores are made of this material. HD bags are prone to creases and wrinkles, they make a clear rustling noise when rubbed (so called foam bags). They are often made thicker to limit the above disadvantages. And it is also these disadvantages that this material is relatively cheaper than LDPE plastic.
The production process of HDPE plastic bags is similar to LDPE, but there is a slight difference in the machinery system. Specifically, the mold head used to shape plastic bubbles has an additional central stabilizing bar. This central stabilizer bar blows out surrounding airflows that keep the plastic bubble upright, while cooling the inside of the membrane. This difference is due to the fact that HDPE has a higher melting point (130-150°C) and the temperature of the new extruded plastic film is very high and needs to be cooled quickly.
Production process for PP
PP plastic belongs to the polymer family, is a high-quality material and is more expensive than LDPE and HDPE. Plastic bags made of PP material are very uncommon, mainly used to contain high-cost products or need packaging with rigidity or transparency.
PP plastic bags are colorless, odorless and non-toxic, extremely safe to store food. An interesting feature of these materials is that they easily tear when there is a hole or a small tear. Therefore, PP plastic packaging is also often used to contain products that when needed, consumers only need to tear off the outer layer. Balloon bags containing fresh flowers are an example. PP bags also have very good heat resistance due to their high melting point, about 160-171°C.
Also because of such a high melting temperature, the production process of this type of packaging must completely change. The temperature when blowing the film is high and wide with the heavy density of the material, which makes the PP plastic film unable to be blown from the bottom up. Air bubbles will easily tear or be deformed. Instead, people use the method of blowing from above. In addition to the cooling method from the inside, people also let the water flow continuously onto the bubble layer to cool them quickly. The PP film layer, after being completely cooled, is rolled into a paper core in the same way as other materials.
In addition, the above types of plastic bags can also go through a number of stages to become finished products. For example, punching holes to make handles, punching holes for ventilation or grafting on two ribs to become a zipper bag, cutting a seal to make a mouth bag, etc. However, in general, all types of plastic packaging are used. produced by extrusion-blow-pressing and cutting out into bags. Only differ in a few stages or special processing steps depending on the requirements of the product.
SUNRISE COLOURS VIETNAM CO., LTD
Add: CT2A Building, Gelexia Riverside Apartment, 885 Tam Trinh Street, Yen So Ward, Hoang Mai District, Hanoi City.
Phone: +84 986998350 Fax: 0084 02436452586
Moblie/What'sapp/Wechat: 84 986998350
Email: sales3@sunrisecolour.com
Website: http://sunrisecolour.com
Related posts
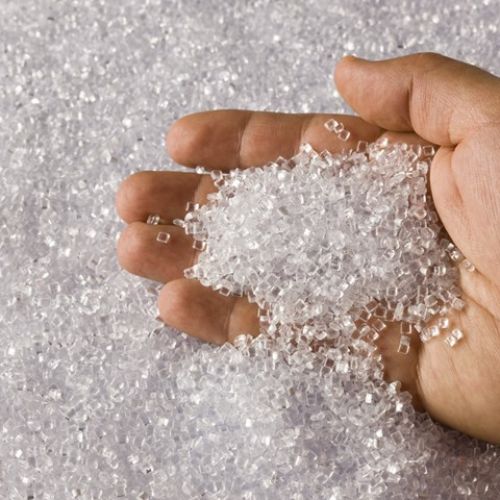
.png)
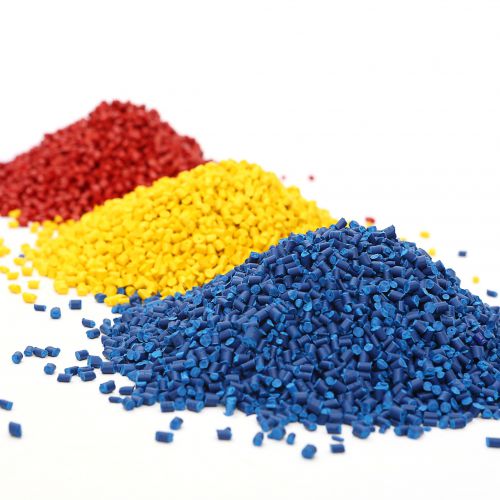